Particleworks - Features
Co-Simulation of Rigid Dynamics and Fluid Dynamics
RecurDyn’s unique ParticleWorks interface allows you to easily perform co-simulation of solid and fluid dynamics.
hrough co simulation with RecurDyn, ParticleWorks allows you to capture the effect of fluids interacting with mechanical systems.
Key Features
- Meshless (Meshfree) CFD software based on particle method
- One single easy-to-use interface from CAD import to post-processing
- Tight 2-way coupled simulation with RecurDyn (rigid and flexible bodies)
- Surface tension (CSF model and Potential model)
- Turbulence with the hybrid model i which LES(Large Eddy Simulation) is combined
- Heat transfer between solids and fluids, temperature-dependent viscosity
- Free surface flow, large deformations
- Viscosity (Newtonian/Non-Newtonian fluids and high-viscosity fluids)
- Air resistance using the external data (useful to analyze the mist or spray with air resistance)
- Implicit/Explicit Methods
- Various Boundary conditions (Wall, Inflow, Moving, Periodic)
- Direct file import form CAD software
- Optimized for the latest Multi-core CPUs and GPUs
- Coupled simulation including fluid, powder and rigid body
Pre-processing / Post-processing
Particleworks allows you to directly import 3D data from CAD software for defining the volume boundaries. Various boundary conditions and material properties can be applied to imported data. You can view or output the simulation results in various formats.
- Pre-processing
- Import 3D data from CAD software (STL format).
- Generate fluid particle sources and sinks (through circular, rectangular, or arbitrary shapes).
- Import 3D data from CAD software (STL format).
- Post-processing
- Contour plots.
- Streamline plots.
- Animation of fluid motion.
- Output coordinates, velocity, pressure, shear rate, torque, etc. in various formats.
- View or output the simulation results as image (JPEG / PNG), video (MPEG / AVI) or STL files.
- Contour plots.
Solver
Since the fluid dynamics solver uses the MPS method, it allows you to mix various material properties of fluid, rigid, and powder. (However, the rigid-powder mixing is not supported.)
The solver also allows you to calculate shear rate and torque, etc. from velocity, pressure, and temperature of fluid.
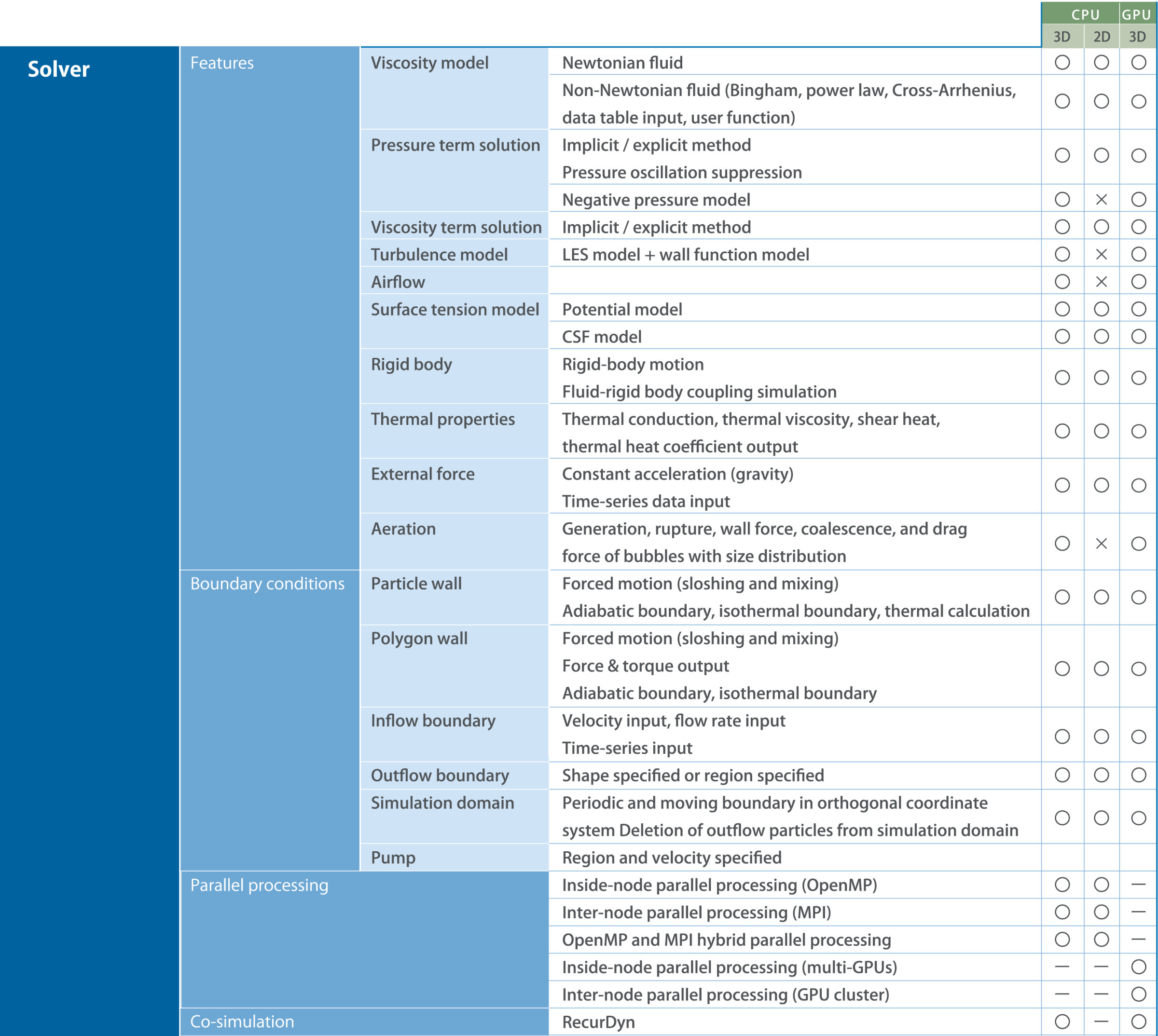
Optional Functions
Advantages of Co Simulation
Mesh-free Simulation
<Crankshaft oil lubrication simulation>
Source & Sink
<S-pipe flow simulation>
Particleworks has the ability to generate particles and remove particles during the simulation using sources and sinks. This allows users to easily model the flow through, for example, a pipe, allowing you to simulate complex systems easily and reduces the simulation time greatly.
Viscosity consideration
<The effect of viscosity>
Particleworks also models the effect of viscosity. The viscosity can vary with conditions such as temperature. This enables you to identify the effect that fluid type or temperature have on the coupled fluid-solid system.
Coupling with the RecurDyn/MFBD
<The effect of viscosity>
Particleworks supports the interactive simulation with the flexible bodies of RecurDyn. (bidirectional coupling) R-Flex (linear elastic bodies) as well as F-Flex (nonlinear elastic bodies) with large deformation can be reflected in real-time to polygon wall in Particleworks and Granuleworks. Simultaneously, RecurDyn calculates the deformation, dynamic stress and strain under the fluid force calculated by Particleworks.